文 | 来源·上海东方久乐汽车安全气囊有限公司 湖南车市
继1952年美国John Hetrick和1953年德国Walter Lindner发明汽车安全气囊后,安全气囊技术日新月异,20世纪90年代后,美国、欧盟、日本已正式立法在汽车上配置安全气囊,双安全气囊已经成为绝大多数主流轿车的标准件。在汽车发生碰撞时对车内乘员直接起保护作用的是安全气囊中的气袋,因此气袋是汽车安全气囊中至关重要的零部件之一。
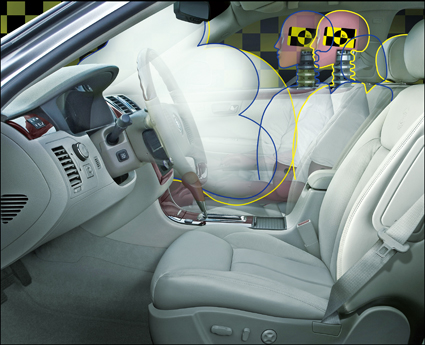
影响气袋保护效果的因素
气袋是由柔性材料制成的密封袋,它接受来自于气体发生器总成的气体,用以保护乘员避免与车内部件相撞。当汽车发生碰撞时,车内的ECU检测出碰撞信号并点燃气体发生器,气体发生器产生气体给气袋充气,气袋从饰盖中展开保护乘员,一定时间后,气袋的气体逐渐释放,保护过程完成。
气袋可以根据安全气囊的类别来进行分类。主要可以分为以下几种:驾驶者安全气囊气袋(DAB气袋)、乘员侧安全气囊气袋(PAB气袋)、侧面安全气囊气袋(SAB气袋)、侧面安全气帘气袋(CAB气袋)以及膝部安全气囊气袋(KAB气袋)等。
气袋的保护效果在结构方面主要受气袋的包形、拉带、排气孔这三个主要的参数影响。
气袋的包形是指气袋经过裁剪并按照一定的方法缝制后实现的气袋形状,在车辆碰撞并对气袋充气后,气袋的包形对乘员的保护范围、保护角度、以及伤害值都有影响。但是由于每款车的设计不同,仪表板的位置、座椅的设计、转向盘的设计等等的差异性决定了配装每款车的包形有所区别。目前,一般来说,DAB气袋的包形是圆形,PAB气袋的包形是长方形,SAB气袋的包形也是近似长方形居多。
目前的气袋中普遍使用的一种设计就是拉带式气袋。所谓拉带式气袋就是气袋的内部缝制一条或几条拉带,通过这一条或几条拉带来控制气袋的展开厚度,微调气袋的展开方向。大多数DAB气袋中都会使用拉带,有部分PAB气袋中也会使用拉带来控制。
排气孔是气袋设计中的重要设计内容之一,基本上每个气袋都有一到两个排气孔,排气孔的作用是调节气袋充气压力。车辆碰撞瞬间,乘员撞击已经打开的气袋,迫使气袋内气体从排气孔排出以吸收乘员冲击的动能,达到保护效果。在设计气袋时,若排气孔设计过大,则有可能气袋无法起到保护作用,或者作用时间不够,气袋就快速泄气结束;若气袋排气孔过小,会造成气袋内压力过大而使得气袋爆裂失效,或者乘员撞击气袋时不能及时泄气吸收动能,间接对车内乘员造成伤害。在设计并验证气袋时,调节排气孔来微调气袋是最常见的手段。
气袋的原材料主要有气袋布和气袋缝纫线组成,由于安全气袋的特殊作用,因此对于气袋布和缝纫线都有较高的要求。
气袋布主要性能
安全气囊气袋布的材料选择主要考虑以下几点因素:能承受气体发生器产生的热空气能量;能阻止灼热粒子击穿布料;要能够使得气袋从模块中顺利钻出并展开;阻止乘员大幅运动/吸收撞击所产生的能量;在-35℃到+85℃的条件下折叠并压缩保存15年不失效;可以折叠成较合适的体积放在安全气囊的模块内。
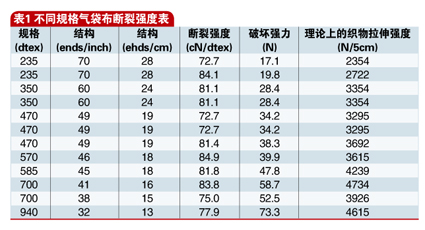
对于以上几点要求,在选择气袋布时应关注以下几点材料性能:
断裂强力:断裂强度不够,安全气囊引爆时气袋布断裂引起气袋失效,气袋布纱的规格越高则断裂强度越大,见图3。对于气袋布断裂强度的选择取决于气袋的设计,不同类型的气袋断裂强度不同。纱线的规格降低,并且增大纱线经纬的密度都可以使断裂强度增大。从图4可看出,同样的一款布料,密度41×41的断裂强度明显比密度38×38的要大。
撕裂性能:撕裂性能不够,安全气囊引爆时气袋布被撕裂引起气袋失效。织物的撕裂性能和纱的拉伸强度、织物的结构以及纱线之间的摩擦力有关系。粗纱织成的布料撕裂强度较高,纱线密度增大,布料的撕裂强度降低,纱线之间的摩擦力减小,布料的撕裂强度增大。
气密性:气密性差,气袋保气性差,会引起气袋内气压不够或者保气时间不够,保护失效。涂层织物的气密性很好,非涂层织物气密性比涂层织物低。
缝接强度:缝接强度差,安全气囊引爆时会使得缝合处撕破。气袋布的缝接强度和织物的结构以及纱线之间的摩擦力有关系,增加气袋布的密度会提高气袋布的缝接强度,但是同款规格同样密度的气袋布,涂层的缝接强力比非涂层的要小,这是因为涂层的硅胶减小了气袋布的摩擦力,使得它变得很滑。
老化性能:老化性能不够使得气囊袋在车内一段时间后失效。可通过环境试验来模拟织物,验证织物的老化性能。
温度变化性能:温度变化性能差,使得气袋布装车后经过各种温度变化后,性能下降,引起气袋失效。
目前气袋布的原材料主要使用PA6.6的丝织造。常用的规格有350dtex、470dtex、580dtex、700dtex等,规格越高,所能承受的力越大;气袋布根据气体发生器的出气能量还可以选择涂层和非涂层的,涂层气袋布有更好的保气性和隔热性能,但是会使气袋布的厚度增加,增大对安全气囊模块装配空间的要求。因此,在选择气袋布时要综合考虑气袋布的性能、气体发生器的性能、以及折叠后的空间要求,选择一款适合的气袋布。
近年来,PA6.6原材料的需求增大,价格攀升,人们一直在寻找一款性能近似,可以替代尼龙气袋布的材料。涤纶气袋布是近年来各大安全气囊厂家不断尝试的新气袋布品种,它的性能与PA6.6近似,并且价格便宜,产能大,但是老化性能和耐热性能方面较尼龙气袋布有一定的差异,有待进一步改善。
缝纫线:对安全气囊的缝纫线的要求主要有以下几点。
对气体发生器产生的热空气能量承受能力、耐摩擦性能、色牢度、良好的缝纫性能,最少的跳针、跳线以及断线情况、良好的股纱巩固能力、合适的延伸率。
缝纫线和气袋布一样,原材料主要使用PA6.6,有小部分会使用PA4.6的原丝。PA4.6的原丝比PA6.6的原丝有更好的耐热性能。除了原材料外,影响气袋缝合效果和性能的因素还有缝纫线的制作工艺、缝纫针的配合、缝纫机器的调整以及缝纫工人的操作等。这些因素的完美配合会有良好的缝合效果以及缝纫性能。
目前国内外制作安全气袋普遍使用两种线迹——301平缝线迹和401双针链缝线迹。301平缝是最常用的针步,它具有转弯方便、缝线紧密、针步外型平坦并且不容易散开等特点。此外,利用301平缝还可以进行倒针,免除了缝步散开的风险。但是301平缝需要定期更换底线,影响生产效率,且缝步的弹性比401链缝针步差。401双针链缝的优点也很多,主要有:1)无需更换底线——减少车缝返工;2)较强的缝步拉力——减少缝步爆裂;3)较强的缝步弹性——减少缝步爆裂和增加缝步弹性;4)较高的车缝速度——可以增加生产力效率。401双针链缝的特殊针步结构决定了401的针步很容易被散开,容易被拆解。
目前气囊行业中,301线迹主要用于气袋的进气孔和放气孔以及拉带的缝制,401线迹主要用于外周缝纫以及需要加强的加强片等。用301针步缝纫进气孔和放气孔,使得进气孔和放气孔缝合紧密,遇到高温缝线不易散开。401针步缝纫外周则使得外周可承受较强的拉力,并且增加了缝步的弹性。
气袋发展的新技术
随着科技的进步和人们对汽车安全重视程度和技术要求的提高,对气袋的保气时间、保气压力等要求也不断提高,应运而生的的气袋新技术主要有气袋密封胶技术(Seam Sealing)、一片式织造气袋技术(OPW)。这两种新技术的特点都是具有良好的保气保压能力,对汽车翻滚事故中保护乘员具有良好的效果,主要应用在侧面气帘安全气囊(CAB)气袋上。
气袋密封胶技术就是在气袋缝纫之前在缝纫的轨迹上涂上一层密封胶,密封胶和气袋布内部的涂层结构紧密结合干燥后,再进行缝纫。在气袋展开时密封胶先受力,再缝纫线受力。这样可以增加保气时间,实现翻滚保护。
一片式织造气袋技术(OPW是one piece woven的缩写,意思是一片式织造)在织造过程中两层面料同时加工,充气区域在织造过程中形成。
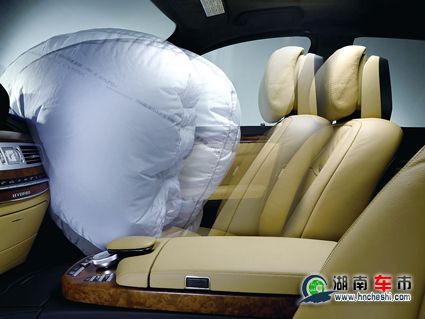
上图是OPW的气袋结构放大示意图,从图中可以看出,OPW气袋在织造的时候,把需要充气的区域直接织成了两层,把不需要充气的区域织成了一层。织造结束后在气袋外层(正面和背面)分别进行涂胶,最后按照气袋的包型在裁剪机器上裁剪。
目前国内汽车中安装的OPW气袋都是从国外进口的,国内目前还没有OPW的成熟织造技术厂家,厦门的华懋公司等正在进行技术准备。在亚洲有三家成熟的OPW的织造生产商,一家是日本的丰田合成;一家是韩国的可隆公司;另外一家是日本的SAS公司。奥托立夫在OPW方面申请有技术专利。
近年来,气袋检测技术方面也发展迅速。首先,在气袋裁片上,为了区分气袋布的正反面,气袋布供应商使用了喷码技术,在气袋布的正面喷码,这样既便于追溯又可以区分正反面,这种方法对于非涂层布的辨识特别有效。其次,气袋裁片缝制成半成品时,在气袋缝制半成品的关键位置印上墨点,气袋缝制好后,检验员根据墨点的尺寸对比检测气袋缝制是否正确,尺寸是否合格以及折叠是否正确。现在一些气袋工厂还利用色差检测仪器来检测气袋的尺寸和缝制。
汽车安全气囊已经成为现代汽车的重要标志之一,它是一个迅猛发展的高新技术产业,目前世界上绝大多数的主流车已配置安全气囊。在我国,越来越多的人开始重视汽车安全问题。但是我国的安全气囊研发人员和设备缺乏,在本土生产的安全气囊企业中,80%以上是外资背景的,关键技术一直掌握在外方手中,我们自有的安全气囊技术匮乏或者处于摸索阶段,这是我国安全气囊研发极需解决的问题。加入WTO后,我国现行的组装式和仿制式安全气囊在技术和经济上将面临严峻的国际竞争。因此,在安全气囊研究方面有所创新并拥有自己关键技术的知识产权,才是中国安全气囊发展的立足之本。